With over 30 years of trusted reputation, Dimatec crafts high-value cost-efficient metal parts used in the oil and gas, drilling, mining, agriculture, transportation and energy sectors.
Dimatec’s Machining Division brings your vision to life since 1988. From small to large production runs, top-notch technology, innovation and competitive prices to meet your needs for custom order fabrication.
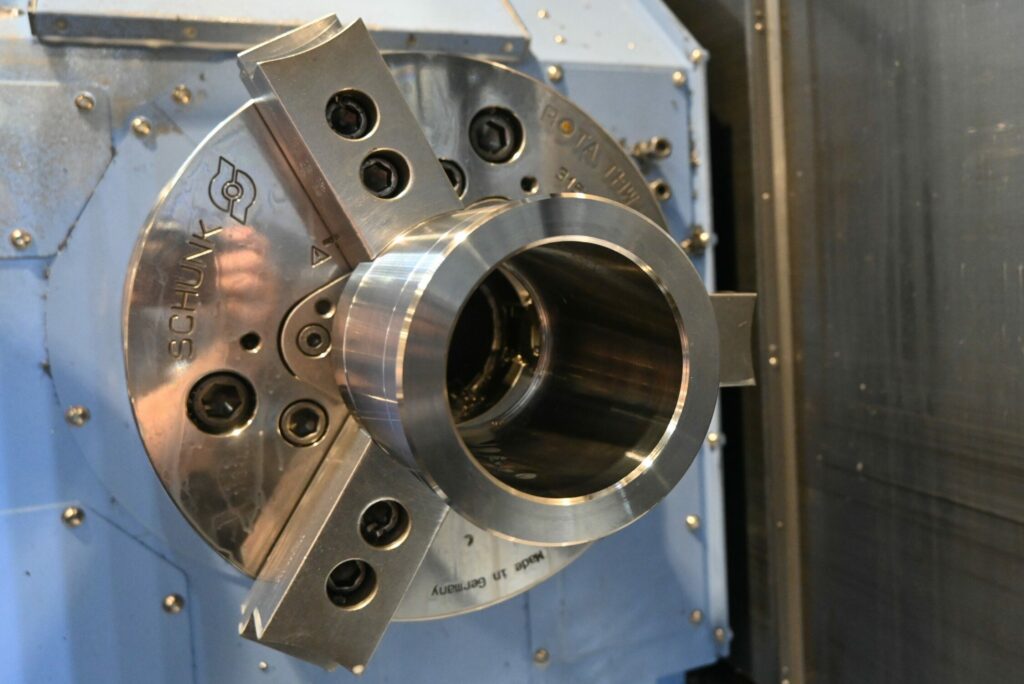
- Lathe Turning
- Machining Centers
- Drilling
- Surface Grinding
- Induction Brazing
- Welding
- Sand Blasting
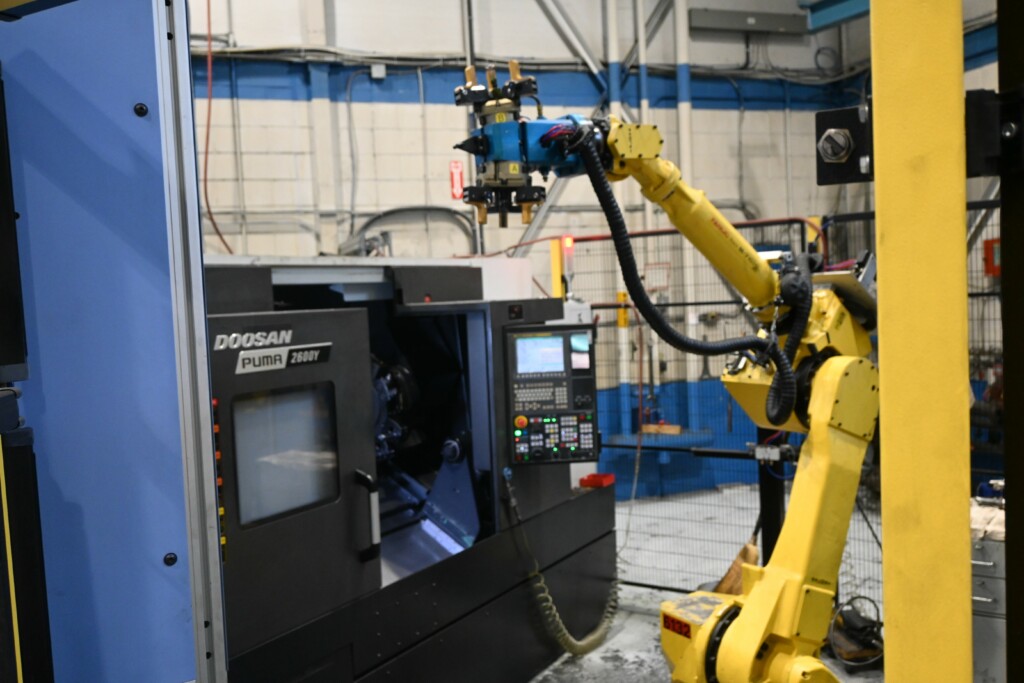
- Innovative Manufacturing
- Enhanced Productivity For Medium to Large Productions Runs
- Controlled Process
- Cost Reduction
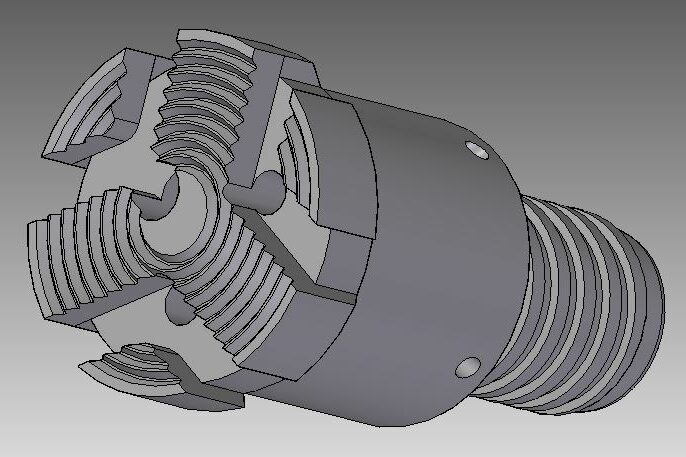
- CAD
- CAM
- Prototyping
- Research and Development Services
What is your wishlist? We help you grow your business. Our R&D department will bring your vision to life. Here we make it right.
In our +40,000 ft2 facility in Winnipeg, Manitoba, we utilize 20 Computer Numerically Controlled (CNC) 2-to-9 axis machining centers run by highly skilled machinists or integrated with robotic automation.
Our maximum machining size capabilities include a Max. OD=Ø18.0”, Max. ID=Ø16.0” and Max. Length= 60.0”. Tolerances are gauged to .0005 and confirmed on a Coordinate Measuring Machine (CMM).
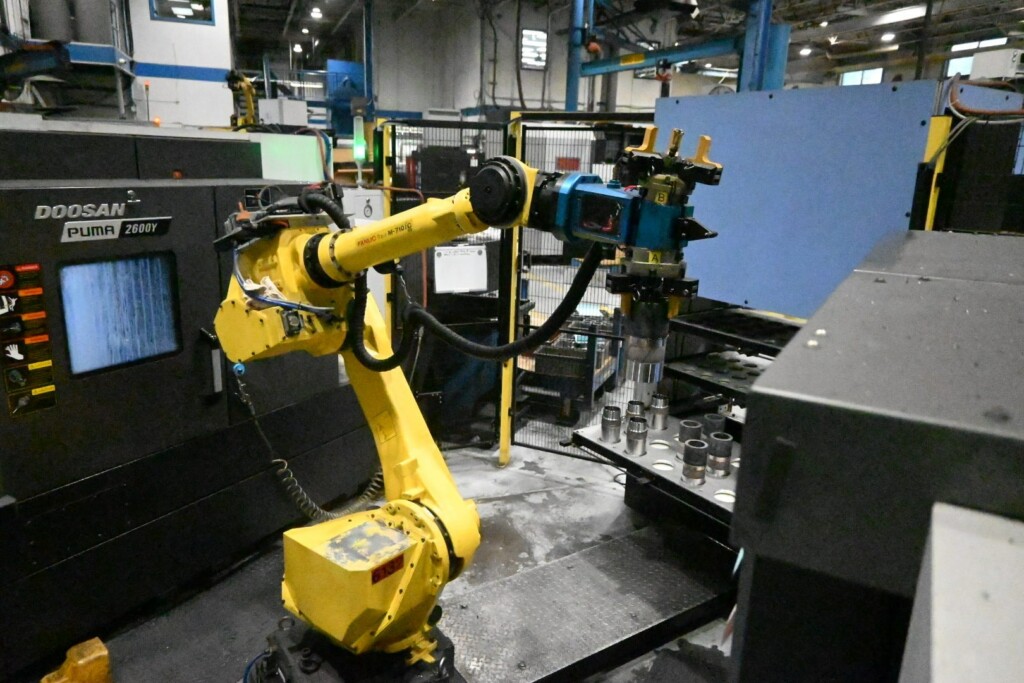
A fully automated cell with robot load/unload capabilities meant for high production runs for medium complexity of parts.
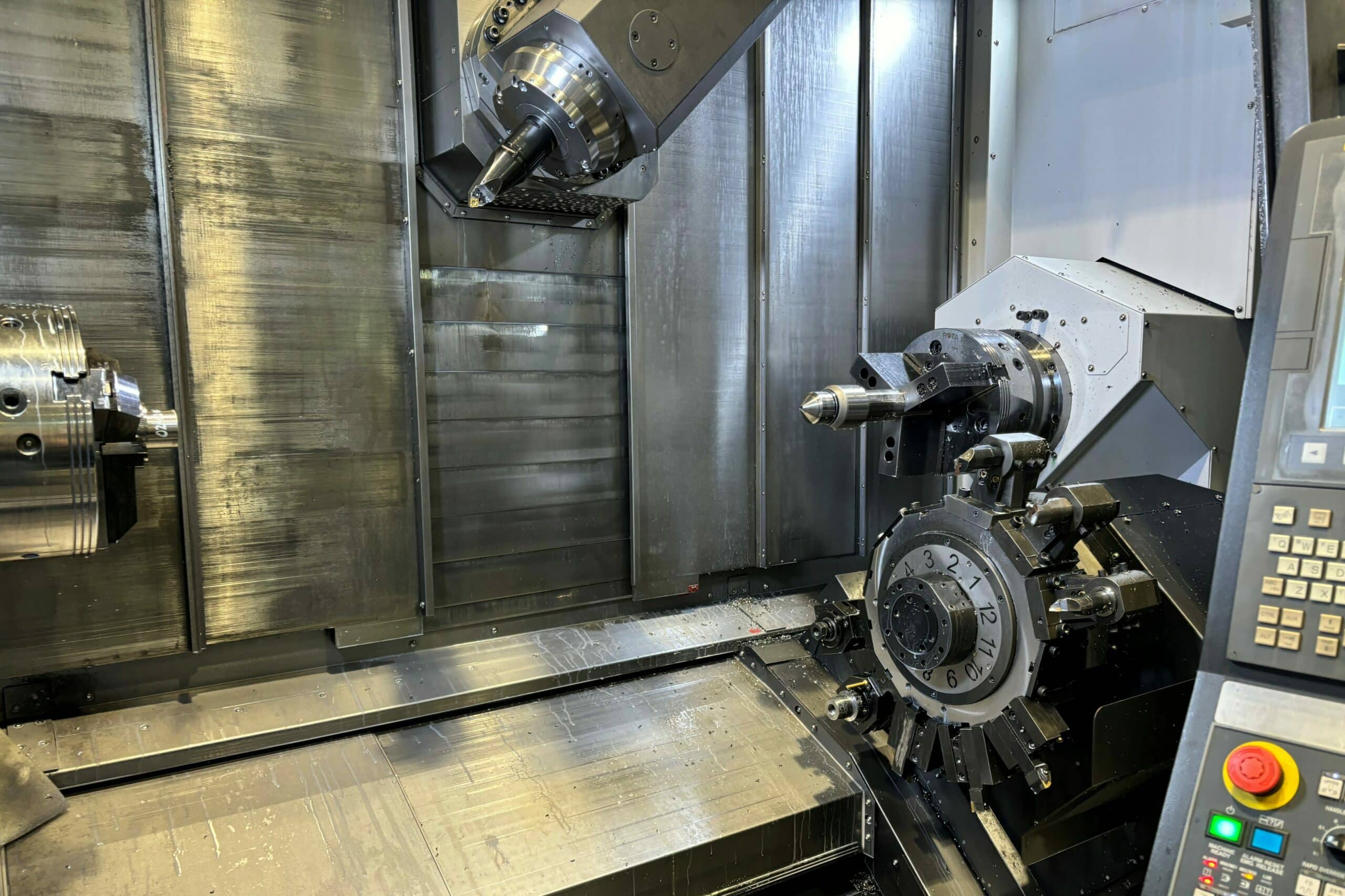
Ready to make the most complex parts with intricate geometries, precise tolerances and features utilizing the versatility of the equipment to perform a wide variety of operations such as turning, milling, drilling, tapping all in one machine.
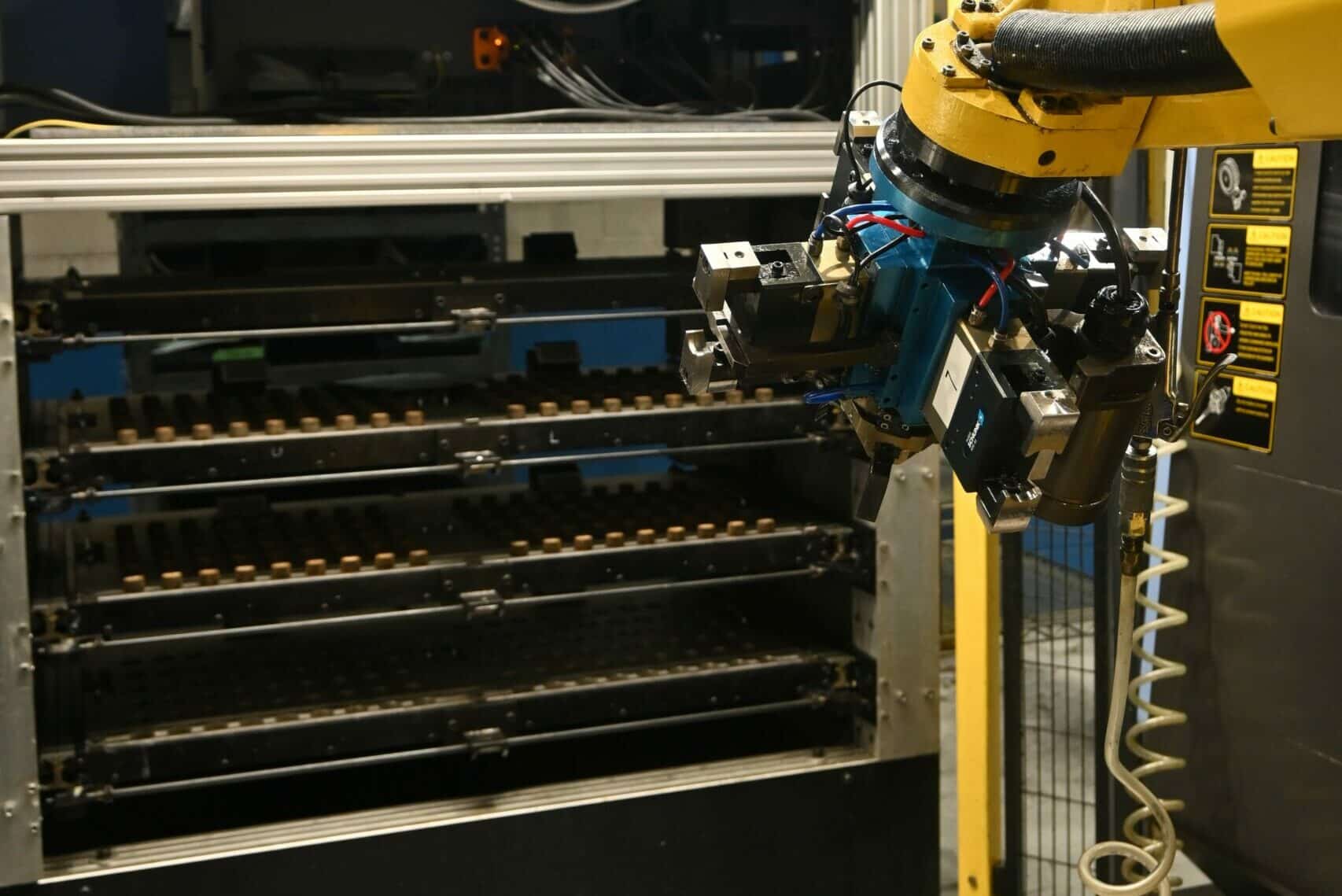
A fully automated cell with robot load/unload capabilities meant for high production runs for complex parts. The cell features Renishaw measurement capabilities with self-calibration allowing in-process measurement along with self-adjustment using Statistical Process Control (SPC).
Dimatec offers a range of additional in-house special processes that include:
- Surface wear protection solutions through the integration of powdered metal matrix-bodies into steel components
- Surface treatments such as Zinc-Phosphate and anti-corrosion coatings on steel components
- Shot peening of external and internal thread connections
- Cold thread root rolling of API rotary shouldered connections in compliance with the requirements of ANSI/API Specification 7.2:2008 and ISO 10424-2:2007
- Automation – Robot load/unload – In process measurements
- Non-destructive testing (NDT) in the form of liquid dye penetrant inspection (LPI) using either the post emulsion fluorescent process or the visible dye water washable process, depending on the physical size and shape of the component being inspected.
- Dimatec has a registered quality management system that complies with the current standards set out by ISO (International Organization for Standardization) in ISO 9001:2015.
Do you still have questions?
Send an email to info@dimatec.com or call 1-866-202-5875 (Toll free in Canada and U.S.A.)
or use the form below.